New concept for machining
of „TORX®“ shapes
New concept for machining of „TORX®“ shapes
One drill, one milling cutter, one perfect machining strategy and optimal adapted parameters: the result is a clear improvement of efficiency when machining medical screws of Titanium, Stainless Steel or Cobalt Chrome.
The chosen carbide, coating and mainly the two, respectively three different geometries for Titanium, Stainless Steel and Cobalt Chrome support high cutting speed, high precision of profiles and a nearly burr free result.
CrazyDrill Hexalobe with two cutting geometries for Titanium or Stainless Steel and Cobalt Chrome is available for profiles in the range of T4 – T30 (drill diameter from 0.90 to 3.80 mm, [.035“ - .150“]) or with different dimensions on request.
CrazyDrill Hexalobe Flat with one cutting geometry for Titanium, Stainless Steel and Cobalt Chrome is available for profiles in the range of T4 – T30 (drill diameter from 0.90 to 3.80 mm, [.035“ - .150“]) or with different dimensions on request.
CrazyMill Hexalobe with three cutting geometries for Titanium or Stainless Steel or Cobalt Chrome is available for profiles in the range of T4 – T30 (milling cutter diameter from 0.20 to 1.00 mm, [.008“ - .039“]) and in two lengths: short version 3.5 x d, long version 5 x d. Depending on diameter with 3 or 4 flutes.
The machining process with CrazyDrill Hexalobe, CrazyDrill Hexalobe Flat and CrazyMill Hexalobe
Beside the optimal tools, an adapted machining strategy with correct parameters is also important for success.
Mikron Tool recommends:
- Titanium and Stainless steel: a helical interpolation (three axes) or side milling (two axes)
- Cobalt Chrome: lobe drilling with following helical interpolation (three axes or side milling (two axes)
Each procedure has its pros and cons which can vary depending on the machine. Best is to determine the most successful process with tests.
- Pros/Cons helical interpolation: there will be a slight lateral load at the milling cutter (Fx), since there is also a simultaneous vertical stress (Fz). A higher stress on the cutting edge corners has to be reckoned with and because of this they were geometrically reinforced - faster and more fluid operation.
- Pros/Cons side milling (or wall milling): the total depth is reached in several steps, since only two axes are used for each step. The step-over stays the same for the entire operation even though the radial stress on the cutter is more elevated.
For screws in Titanium the time-consuming milling operation can be done with helical interpolation (with max. pitch 0.8 x d) or with side milling (with stepover max 0.5 x d).
When machining Stainless Steel, the screws can be milled with helical interpolation (with max. pitch 0.8 x d), after lobe drilling, or with side milling (with stepover max 0.5 x d).
Screws in Cobalt Chrome can be machined, after lobe drilling, with helical interpolation (with max. pitch 0.8 x d) or with side milling (with stepover max 0.5 x d).
Machining with helical interpolation for Titanium
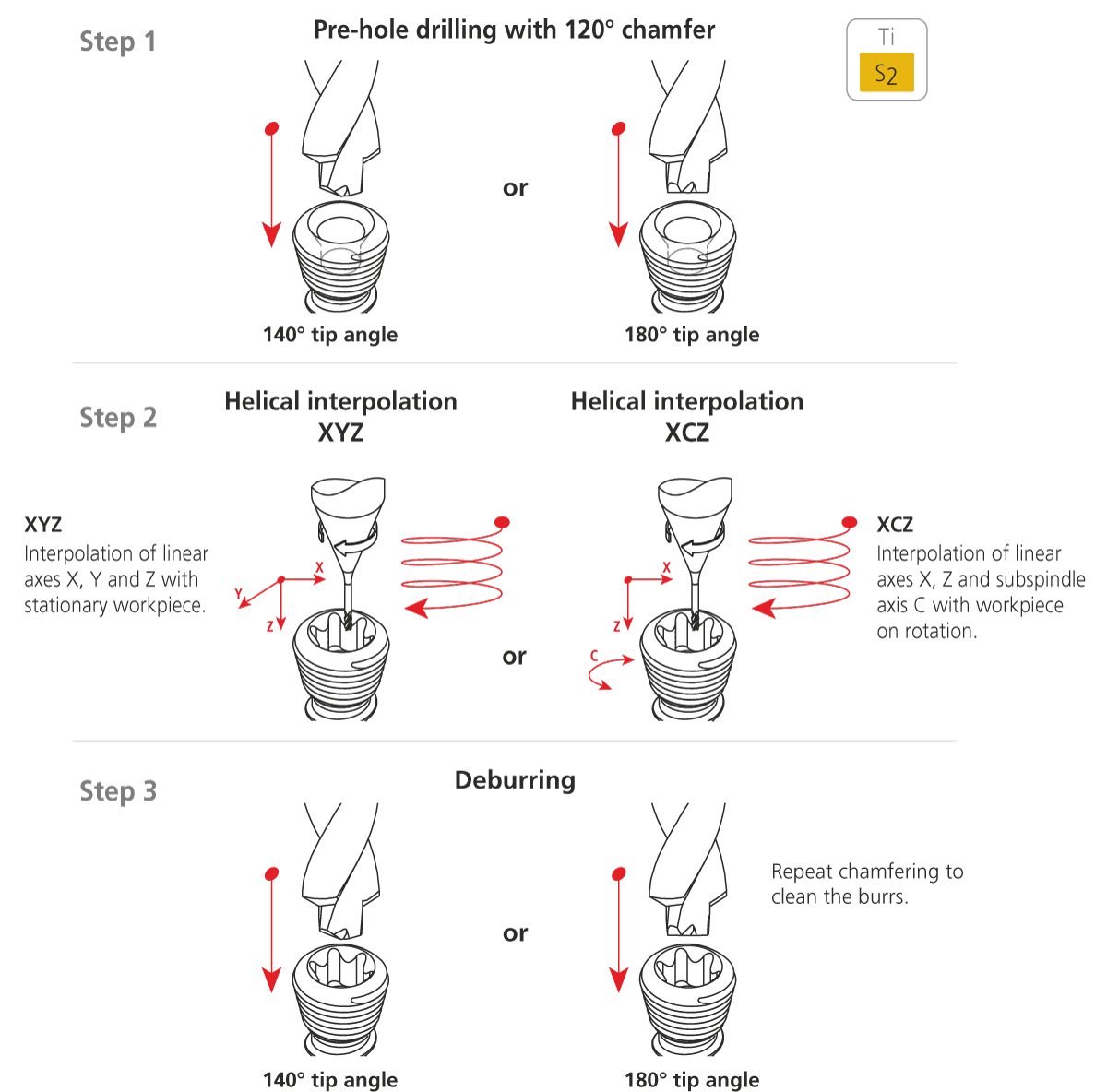
Titanium: In general, helical interpolation is the optimal process for Titanium, time saving up to 20% is possible compared to side milling.
Lobe drilling and helical interpolation for Stainless Steel and Cobalt Chrome
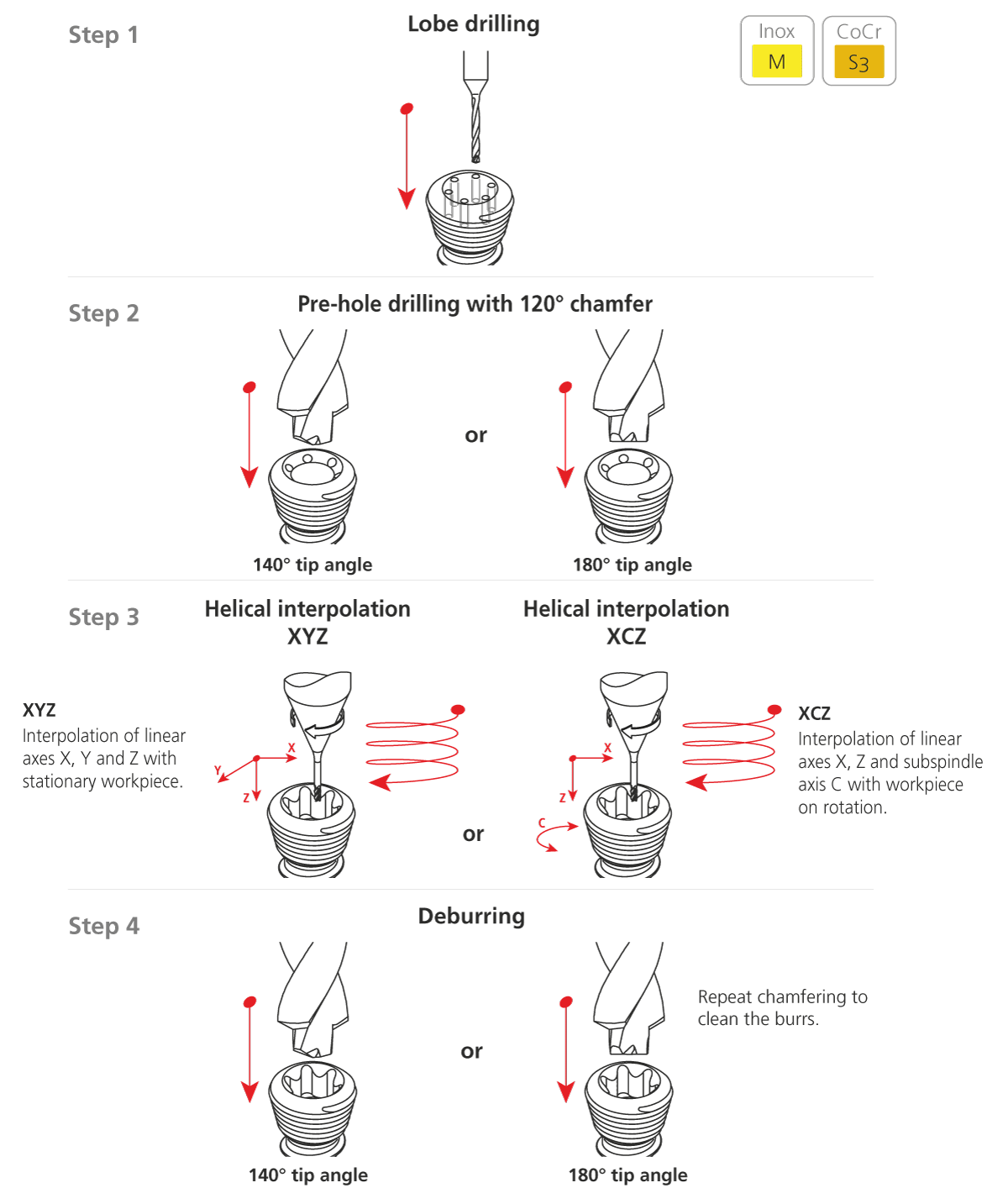
Stainless steel: With helical interpolation, drilling of the lobes is required. Result: longer tool life, better dimensional control of the TORX® shape and a more stable process in comparison to side milling process.
Cobalt Chrome: Helical interpolation is the optimum process, saving up to 20% of cycle time in comparison to side milling process.
Machining with side milling for Titanium and Stainless Steel (Inox)
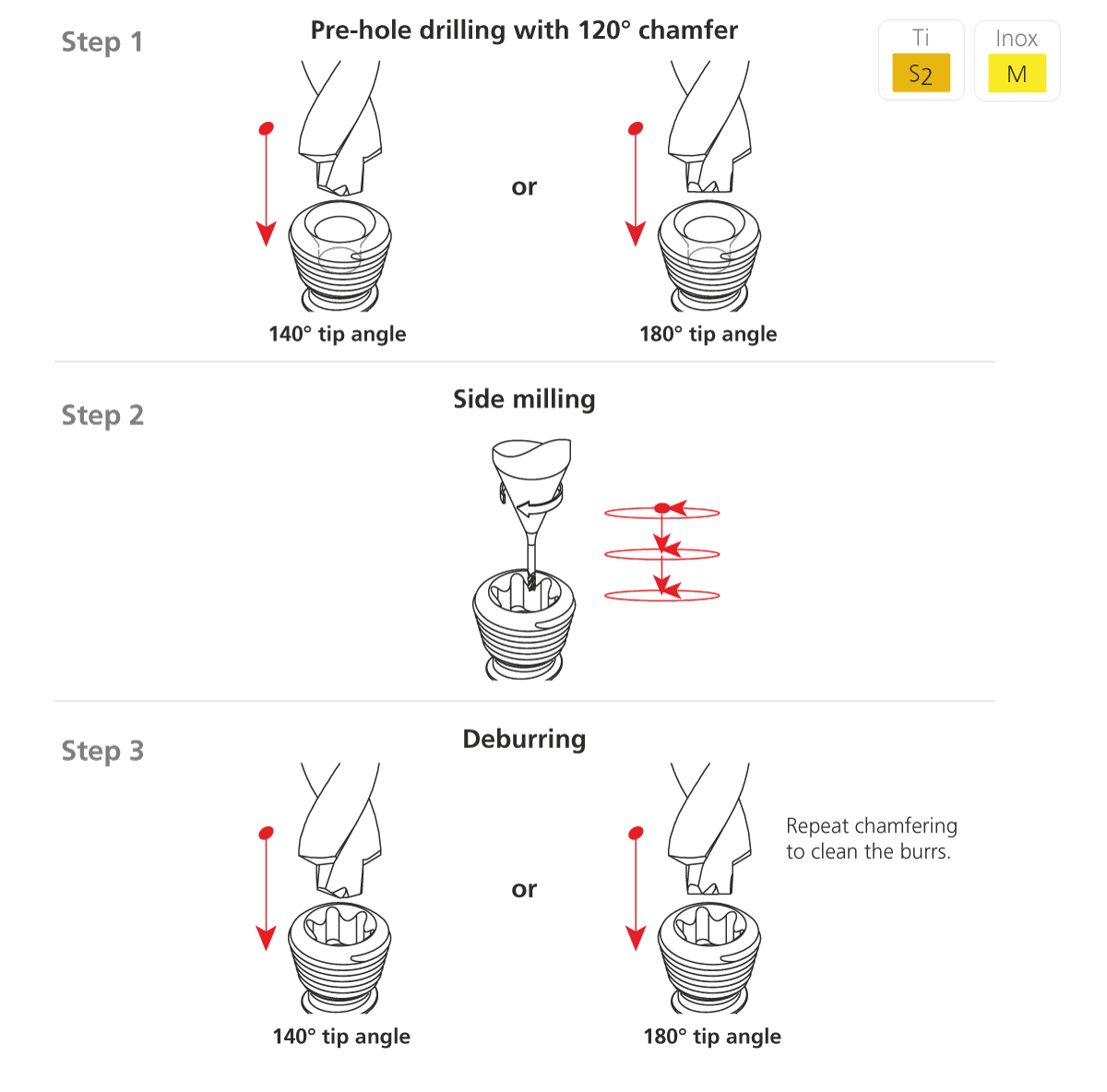
Titanium: Helical interpolation is the optimum process, saving up to 20% of cycle time in comparison to side milling process.
Stainless steel: With helical interpolation, drilling of the lobes is required. Result: longer tool life, better dimensional control of the TORX® shape and a more stable process in comparison to side milling process.
Lobe drilling and side milling for Cobalt Chrome
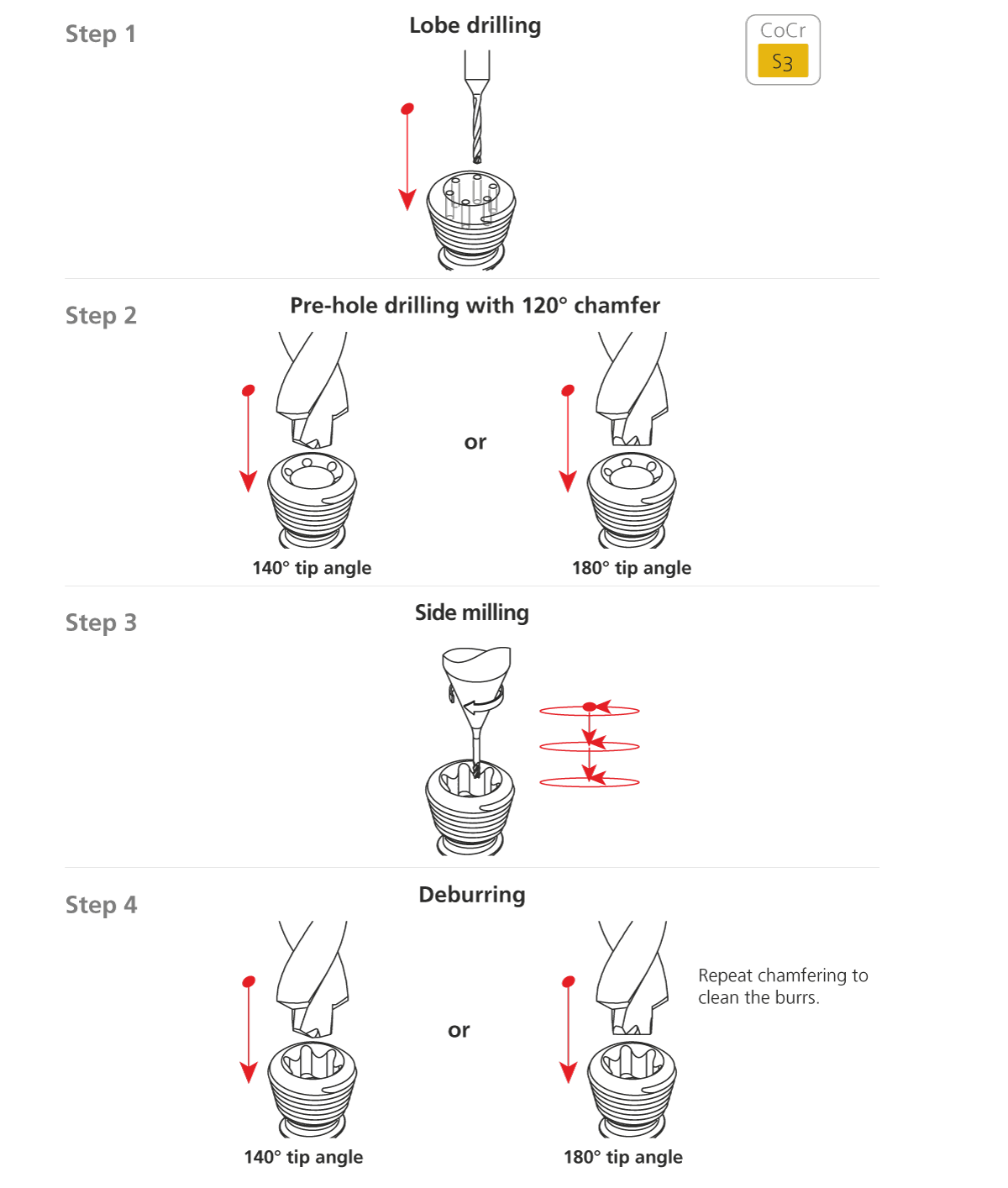
Cobalt Chrome: Helical interpolation is the optimum process, saving up to 20% of cycle time in comparison to side milling process.
Tested and approved
Mikron Tool has determined the ideal cutting parameters (pre-hole drilling and related milling speed to tool life ratio and process reliability) when using CrazyDrill and CrazyMill Hexalobe. These are listed in the cutting data tables according to drill and mill diameter, machining type and material to be machined. The detailed cutting data tested by Mikron Tool, such as cutting speed vc, feed rate f and drilling impact Q, permit a quick and secure machining.
However, the user has to find „his“ balance, specially when milling, between fast machining and long tool life. Also, the exact profile dimensions must be respected during the complete machining time, which has a huge impact on cutting parameters.
The overview of the cutting values table according to material group, material type, hardness and tensile strength, material number, DIN and AISI/ASTM/UNS permits quick determination of the parameters to be used.
Packaging
An impact-resistant and user-friendly drill packaging is absolutely necessary for CrazyDrill and CrazyMill Hexalobe. Mikron Tool offers all tools of the Hexalobe family in a high quality, single package.
Notes or further questions
You can find indications about tool holders, cooling and lubrication under the column "Additional Infos".
Mikron Tool has an international team of cutting technology experts who are pleased to answer your questions (how to use a drill, tools, machines, tool holders, cooling, machining process…).
Use this link to contact us directly.